High-strength mullite castables are used in some important parts such as the front kiln mouth of the rotary kiln, the high-temperature grade discharge pipe, the tertiary air duct, and the tertiary air valve. RS Refractory Materials Manufacturer can provide refractory lining materials for various high-temperature industrial furnaces. During use, the following aspects should be paid attention to when using high-strength mullite castables.
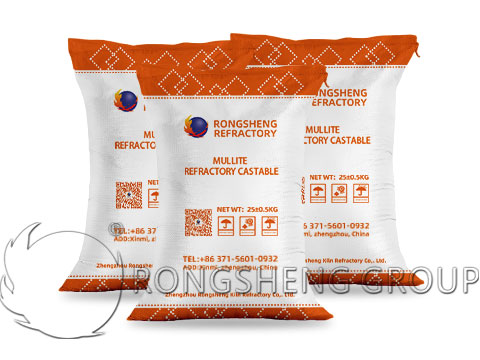
1. Strive to improve the system operation rate of the kiln
The operation rate represents a series of issues such as whether the production is normal, whether the operation is precise and stable, and the number of faults starts and stops. The refractory materials in the precalciner kiln production line are most afraid of kiln startup and shutdown. In particular, the kiln mouth castable is the most vulnerable part to kiln startup and shutdown. The higher the kiln’s continuous operation rate, the longer the castable life. Once abnormal faults such as preheater blockage occur, the surface temperature of the kiln mouth lining will drop from about 1,400°C to 100-200°C in more than 10 hours. After the fault was eliminated, the temperature rose sharply to normal temperature. Such intense alternation of hot and cold is repeated, and the high-temperature structure of the cast body is destroyed and easily explodes and peels off. It has a great impact on the service life.
2. The amount of water added to high-strength mullite castables
Hydraulic castables must rely on mixing water and binders to produce the necessary initial strength, molding, and flow. On the other hand, the amount of water and binding agent is sufficient to achieve this goal. The water consumption must be as little as possible to meet the minimum construction fluidity of various parts. When the lining undergoes high-temperature baking, it will develop high-temperature sintering strength that can withstand the working temperature.
3. Pay great attention to the mixing and homogenization process
The importance of this work is mainly reflected. First, refractory materials will generate certain mineral phases at high temperatures. This is the result of the chemical reaction of various elements inside the lining material. Various high-temperature properties depend on the mineral phase and its degree of homogenization. In the same way, only if the components in the raw materials are uniform will it be conducive to its reaction and the formation of mineral phases. Second, the binding agent and its water can only be dispersed evenly. Only by evenly wrapping the surface of material particles can they condense more tightly and firmly.
The construction process of high-strength mullite castables. Dedicated personnel are responsible for management. Use a forced mixer to mix, no more than 300 kg at a time. All pouring materials including small bags must be poured in before stirring to prevent pouring materials while stirring. Dry mix for about 2 minutes or after visually observing that the color of the castable is evenly mixed, quickly add 70% to 80% of the water. After stirring evenly, check the amount of water, then slowly add insufficient water and continue stirring. The total mixing time should be controlled within 5 minutes, and prolonged mixing should be avoided. To ensure that the castable has good flow plasticity and does not produce an initial setting. The mixed materials are put out at one time to avoid marathon construction that involves mixing and putting them in place at the same time. It also frees up time for the next mixing preparation.
4. Reasonably select and use kiln mouth-guard iron
The main purpose of this work is to effectively protect the kiln mouth cylinder. Protecting the kiln mouth cylinder will ensure the safety of the castable use environment, thereby increasing the service life of the overall kiln lining. Therefore, in many cases, problems with the castables at the kiln mouth are not necessarily due to the quality of the castables themselves. There may be problems with machinery, operation, etc., and it is necessary to systematically analyze and find the root cause of the problem. The general starting point is that under normal operating conditions, the lower the temperature of the kiln mouth barrel, the better.
5. The key is the connection between various processes during maintenance and construction.
Cleaning the castables at the old kiln mouth is labor-intensive and time-consuming, and must be done patiently and thoroughly to ensure that the anchor nails can be arranged and welded as required and that the castables are fully adhered to the cylinder. It is best to use the “Y” type anchor nail with the letter “∪” at the bottom. In this case, as long as the welder’s responsibility is in place, the welding will be firm and there will be no problem. It can also effectively prevent the two supporting corners from being burned and damaged. The expansion joints should be carefully calculated based on the linear expansion rate of the castable material and combined with practical experience. In principle, the number of points and amount left should be few rather than too many to reduce the chance of high-temperature hot air drilling into gaps. All anchors are wrapped with black tape to compensate for their expansion space. Mix the materials evenly to ensure that the castables are not stratified and can be mixed and used to prevent the mixed castables from being left unused for a long time.